PRODUCT INFORMATION
CO2 Extraction Plants (EBU) from Pentair Union Engineering extract CO2 from flue gas from boilers that are fired with fuels such as diesel oil, heavy fuel oil, kerosene, natural gas, LPG, or LNG. The innovative EBU Plants meet the strictest CO2 quality requirements and compared with traditional combustion plants they ensure energy savings of up to 45 %.
LIFE LONG PERFORMANCE
EBU Plants are based on the absorption of CO2 from flue gas into a monoethanolamine (MEA) based solution, which is heated by the steam-heated re-boiler to release the raw CO2 gas.
To achieve the best combination of performance and equipment longevity, a 9% MEA /water solution is used. Under this condition, the optimal balance between CO2 load and avoidance of the corrosive effects of MEA is met.
Result-driven technology – NOxFlash and PUR-D
All our Generating Plants are based on our amine technology, including NOxFlash and PUR-D.
The NOxFlash technology is the result of innovation and research and has been proven in our installations since 2006. The NOxFlash technology:
- Replaces the traditional use of scrubbing with PPM (potassium permanganate) solution thus reducing cost and environmental impact.
- Acts as proven abatement of benzene (aromatic hydrocarbons) in the final product.
The PUR-D technology is the final purification step, consisting of a distillation column, which enables separation/blow-off of non-condensable gasses, reducing the O2 content in the final product to max. 5 ppm (v/v) and obtaining a CO2 purity of min. 99.999 % (v/v).
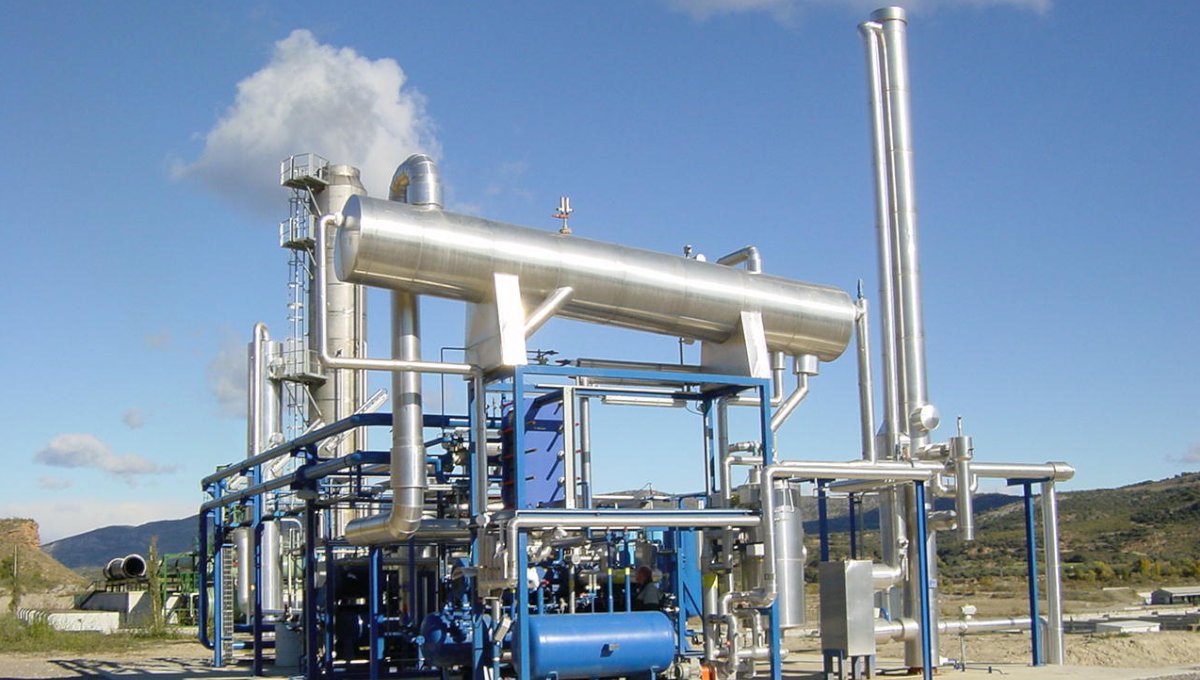
Simple and trouble-free operation
The electrical system for the EBU plant assures:
- The latest PLC technology for operation and monitoring
- Automatic start sequence and fully automatic operation
- Reduced installation and commissioning time on site
The EBU plants are designed for high efficiency and reliability through components selected for 24/7 operation.
-
FUNCTIONAL DESCRIPTION
-
The plant is based on drawing flue gas from boiler exhaust systems. The flue gas will have a CO2 content of 10-14% v/v and is directed to a flue gas scrubber, in which the gas is cooled and water condensed.
The flue gas is directed to a flue gas scrubber, in which the gas is cooled and water condensed. Any SO2 present in the flue gas will be removed by means of a chemical reaction with sodium carbonate (soda ash). The soda ash is automatically added to the scrubbing water through pH control.
After cooling and scrubbing, the gas is led via an exhauster through an absorber, in which the gas flows counter-current to the MEA solution flow. By chemical reaction, the MEA solution absorbs the CO2 from the flue gas. The MEA solution containing the absorbed CO2 (referred to as rich MEA solution) is first pressurized and heated in a heat exchanger and then led to the NOxFlash column. Here most of the contaminants like O2, N2, and NO are removed from the rich MEA solution by flashing to the absorber pressure.
A stream of CO2 and steam is added to the bottom of the NOxFlash column for further reduction of the contaminants in the MEA solution. This optimizes the process yield to the best possible CO2 product without any use of expensive chemicals (Pentair Union patent).
Then the rich MEA solution is pumped to a stripper, where the CO2 is released from the MEA solution utilizing the combustion heat generated in the MEA heater. The CO2-depleted MEA solution (referred to as lean MEA solution) is recycled to the absorber. After exiting the top of the stripper, the CO2-rich gas is cooled in a gas cooler and washed in an after-scrubber for removal of potential MEA carry-over. The gas is then compressed in two stages to approx. 15-18 bar(g) by the CO2 compressor.
Before liquefaction, the gas is dried to a dew point of below -60 °C (10 ppm v/v H2 O) in the dehydrator. Regeneration is done automatically by electrical heating and the use of dry purge gas from the CO2 condenser. Traces (if any) of acetaldehyde are also removed in the dehydrator. The CO2 gas then passes through an activated carbon filter for the removal of any odor substances.
To remove the last non-condensable gases, the CO2 gas first passes a reboiler in the purification system (type PUR-D). It is then condensed at a temperature of approx. -27 °C/-21 °C in a CO2 condenser, where the non-condensed gases are purged off. Finally, the liquefied CO2 is led through the distillation column to an insulated storage tank.
A refrigeration unit, controlled by the CO2 pressure in the CO2 condenser, supplies the matching refrigeration capacity. The liquid CO2 is stored under a pressure of approx. 15-18 bar(g) and a corresponding temperature of approx. -27 °C/-21 °C. During a non-CO2 production period, the refrigeration unit can operate independently of the rest of the CO2 plant to maintain the correct CO2 storage tank temperature/pressure.
The CO2 produced has a purity higher than 99.999% (v/v) and fulfils quality standards as a food/beverage ingredient as specified by International Society of Beverage Technologists (ISBT) and European Industrial Gases Association (EIGA).
-
FIELDS OF APPLICATION
-
CO2 Extraction Plant standard sizes (measured as liquid food-grade CO2 produced):
145 kg/h
285 kg/h
500 kg/h
1000 kg/h
1500 kg/h
2000 kg/h.Other sizes are available on request.
DOWNLOADS
Title | Download PDF | |
Product leaflet | Pentair Union Engineering CO2 Extraction Plants for Boiler Systems - Extraction Based Unit - EBU | Download |
Technical documentation | Looking for operating instructions, installation manual, spare part list etc.? | Please, send us your request |
RELATED PRODUCTS
HAFFMANS CO2 RECOVERY PLANT - CO2MPACTBREW
CO2mpactBrew is a CO2 recovery plant especially designed for smaller, craft-sized breweries with capacity 50.000-350.000 hl/yr.
HAFFMANS CO2 RECOVERY PLANT - CRU
Robust and reliable CO2 recovery solution for a wide variety of brewery needs ranging from 300,000 to beyond 5,000,000 hl/yr.
PENTAIR UNION ENGINEERING ADVANCED AMINE TECHNOLOGY
CO2 capture technology for low-CO2 concentration sources
HAFFMANS CO2 RECOVERY PLANT - ECO2BREW
ECO2Brew is unique in its design to recover CO2 from fermentation processes at larger 24/7 operating breweries, over 2,000,000 hl/yr.
UNION ENGINEERING CO2 SELF-GENERATING PLANTS - COMBUSTION BASED UNIT - CBU
Based on the latest technologies, CO2 generating plants (CBU) from Union Engineering meet the strictest CO2 quality requirements.
HAFFMANS CO2 RECOVERY - SYSTEM ENERGY SCAN
Scan your CO2 Recovery Systems with Haffmans and get detailed information on energy consumption, performance and quality.