- Home
- Case Studies
- Tennents
Industry
Brewing industry
Challenge
Purchasing CO2 from third party sources
Solution
Pentair CO2 Collection & Recovery System
Results
Recovers over 4,200 tonnes of its own CO₂, repurposing 95% of this CO₂ back into its brewing processes
How Tennent's Brewery Collects & Recovers Its Own CO2
Tennent’s required a fully end-to-end CO2 collection and recovery system, allowing them complete autonomy over recovering their CO2 and the capability to utilize it back into the beer production process.
BACKGROUND
Carbon dioxide (CO₂) is an essential component in beer production, required for carbonating beverages, regulating pressure in tanks during fermentation and dispensing, purging oxygen from bottles and kegs during filling, and cleaning and sanitizing equipment.
Like many breweries, Tennent’s Brewery, a Scottish-based brewery, relied on purchasing CO₂, which can pose challenges, such as the environmental impact of transporting CO₂ to the brewery and, depending on the CO₂ merchant market, volatile market prices and supply risks.
Tennent’s required a fully end-to-end CO₂ collection and recovery system, allowing them complete autonomy over recovering their CO₂ and the capability to utilize it back into the beer production process.
“As an environmentally conscious brewery, it was a natural decision to utilize the CO₂ generated in our fermentation process and incorporate it back into our brewing. Thanks to Pentair’s expertise, we could implement the technology. From start to finish, our experience with Pentair was exceptional. They recommended a comprehensive system that allows us to recover our CO₂ and reintroduce it back into our brewing process through a collection capability. With this system in place, we can avoid the fluctuations of the CO₂ market and focus on consistent and reliable operations.”
- Alasdair Hamilton Engineering Manager, C&C Group Tennent’s Brewery
THE SOLUTION
A common practice in brewing is to vent its CO₂ into the atmosphere to release pressure within the fermentation vessels, which, in turn, increases the brewery's carbon footprint.
As a brewery committed to sustainability, Tennent's sought to collect (or harvest) and recover the CO₂ they previously vented. This was when they turned to Pentair for assistance.
Pentair, a process-oriented solution provider with a substantial worldwide footprint in carbon recovery solutions, supplied a complete package that included the collection, recovery, vaporization, and storage of CO₂.
Harvesting CO₂ from Fermentation
The first step for Tennent’s was to adapt its fermentation process from an open (atmospheric) fermentation to a closed fermentation vessel with controlled gas in and out. This change required a significant modification to the existing fermentation process.
Pentair used its Tank Top Valve technology to collect CO₂ gas from Tennent’s cylindrical, conical fermentation tanks (CCT). This innovative design prepares the gas for harvesting and allows simultaneous cleaning of the fermentation tank from the same supply pipe, meaning no additional cleaning piping is needed.
Once the CO₂ is collected from the fermentation tanks via the Pentair Südmo Valve Tank Tops, the gas is directed to the Pentair Südmo Double-Seat Valve Gas Manifold, a centralized gas and CIP (cleaning in place) media distribution system. From there, the gas can be sent to either a foam trap or a vent trap (if the purity of the CO₂ is insufficient for harvesting). The foam trap ensures that the raw fermentation gas is transferred to the Pentair Haffmans CO2 Recovery system foam-free.
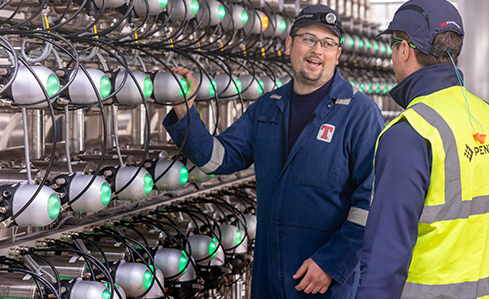
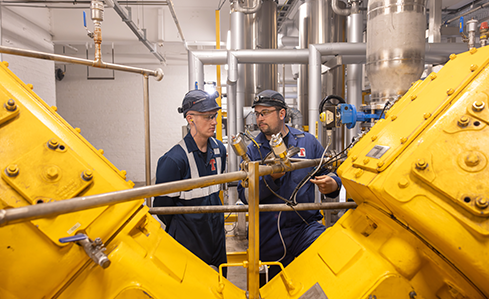
CO₂ Recovery
After the initial fermentation process, the raw, foam-free gas is sent to the CO₂ recovery plant. Here, it is buffered and scrubbed of water-soluble contaminants (like ethanol). The gas pressure is then increased to 18barg (261psig) using a two-stage CO₂ compressor unit, removing condensate. The remaining impurities are removed using a dual-activated carbon filter and drier unit.
At the end of the recovery process, the CO₂ is liquified and stored in a liquid storage tank. From there, the CO₂ can either be exported or sent to the vaporizer, where the CO₂ will be processed into gas form and sent to the CCT and BBT (bright beer tank) area to be utilized back into the brewing process.
Results
Tennent’s Brewery previously needed to buy approximately 4,000 tonnes of CO₂ per year (or 1.8kg of CO₂ per HL) from third-party sources, which they also needed to vent into the atmosphere due to the brewing production process.
TENNENT'S BREWERY NOW
Recovers over 4,200 tonnes of its own CO₂, repurposing 95% of this CO₂ back into its brewing processes and eliminating the need to source CO₂ from third-party sources*.
*Tennent's brewery has not needed to buy CO₂ from external, third-party soruces due to the Pentair CO₂ Collection & Recovery system.
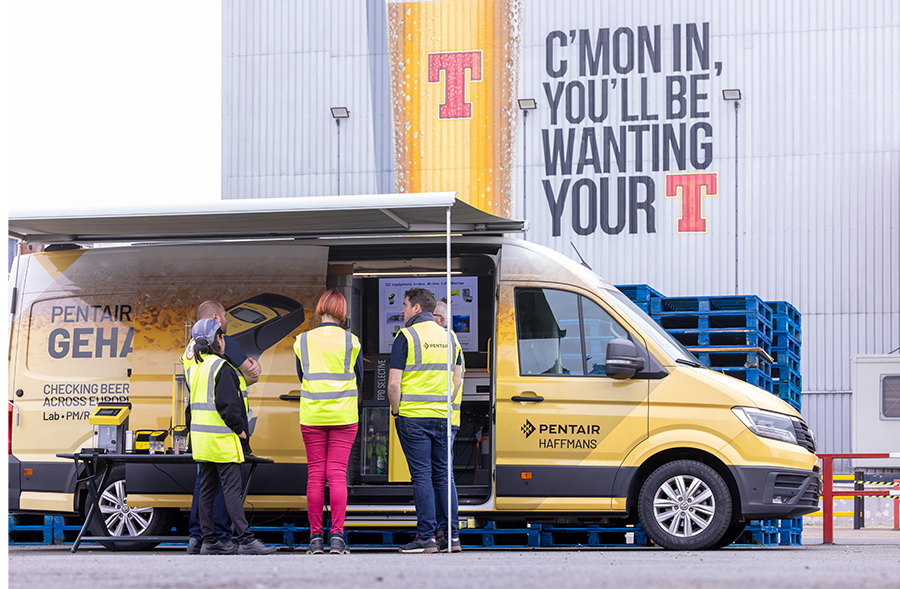
Related Products
Understanding Quality: discover Pentair Haffmans' CO2 management for better taste stability & longer shelf life of your beverage.