- Home
- Case Studies
- Bolten
Industry
Brewing Industry
Challenge
Required a measuring system that could monitor oxygen levels from production to bottling.
Solution
Pentair Haffmans portable oxygen measuring device, o-DGM, which met all their requirements for accuracy, reliability, and ease of use.
Results
The solution allowed for efficient and reliable oxygen measurement.
for the love of the outstanding taste
To meet the increasing quality requirements of today’s beer production process Bolten Brewery uses Pentair Haffmans’ portable O2 Gehaltemeter, type o-DGM.
Whether it is in the choice of raw materials or brewery equipment, the consistent focus on high quality runs like a thread through the 700-year history of Bolten Brewery. Founded in 1266, in Korschenbroich, Germany, Bolten Brewery calls itself the oldest Altbier brewery in the world.
Against this background, in recent years, monitoring oxygen levels from production to bottling has become increasingly significant for quality assurance, as it can negatively affect the flavor stability and shelf life of beer.
The brewery wanted a measuring device that met specific requirements. They needed to measure oxygen at various stations and to be able to measure the oxygen in liquids as well as the purity of gases. In addition, it needed to be independent of the user, offer the utmost accuracy, have reliable measurement stability, and a fast response time. All of this with minimal maintenance and calibration requirements.
“The portable oxygen measuring system o-DGM from Pentair Haffmans fulfilled all of our requirements as a single system. This had us convinced,” - Bolten Brewery Representative.
single or continuous measurement
The device settings allow operators to choose between single sample and continuous measurement. Using single sample measurement, the o-DGM’s portability and light weight make it ideal for routine control during production. In combination with a sampling device, such as Pentair Haffmans ISD 2.0, the inspection of filled containers in the laboratory is much easier.
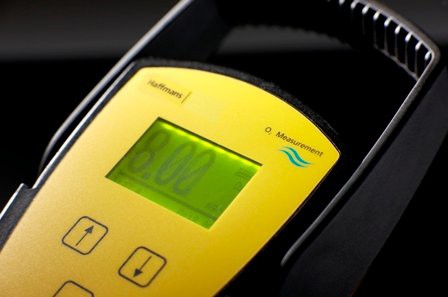
The o-DGM can be used in-line for continuous measurement. The system stores the measured values in the internal memory. Thus, the various production stages can be continually monitored, if in-line measurement is not available or to verify existing in-line oxygen measurement systems. The stored data can be transferred to a PC for analysis.
“The portable oxygen measuring system o-DGM from Pentair Haffmans fulfilled all of our requirements as a single system. This had us convinced.”
- Bolten Brewery
equally suitable for liquids and gases
In addition to continually monitoring beer production, a quality-conscious brewery cannot ignore the examination of product sources such as water and CO2. The o-DGM not only measures the oxygen content of liquids, but also determines the purity of gases. Examples include high gravity brewing where the final product is set using water and CO2 dosaged to the desired parameters and for the inspection of the pressurizing gas in transport trailers. Even the wort ventilation can be controlled through oxygen measurement.
o-dgm
The o-DGM’s oxygen measurement is certified by the TU Munich Weihenstephan and is based on the luminescence measurement. The fluorescence changes in response to the oxygen partial pressure.
Based on the measured oxygen partial pressure and the measured temperature, the amount of dissolved oxygen in the liquid is calculated. This measurement method is completely independent of the operator.
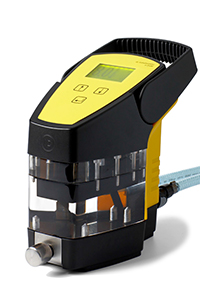
minimum maintenance, fast response time
The optical measurement technology is very stable and does not require regular calibration. Empirically, it was determined that after one million oxygen measurements, the deviation from the zero point amounts to only 5 ppb.
A light pulse counter, which holds the number of exposures, is integrated into the software. When one million measurements are reached, the program prompts you to calibrate the display. This reduces equipment maintenance to a minimum.
The measurement speed is also noteworthy. The luminescence procedure has a response time of approximately 25 seconds, which is many times faster than conventional measuring systems. Thus, the loss of product, such as at the filler can be reduced significantly.
the practical test passed
“The o-DGM oxygen measuring device from Pentair Haffmans has proven its worth in production control as well as a quality assurance instrument in the laboratory and thus represents the perfect complement to our carbon dioxide/oxygen combined instruments, also made by Pentair Haffmans. Thus, the ideal conditions are created, so that the trump card of the Bolten Brewery – the love for the outstanding taste – will stand in the coming years." - Bolten Brewery.
Related Products
HAFFMANS PORTABLE OPTICAL O2 / TPO METER O-DGM
Portable optical O2 / TPO meter combining high accuracy with excellent measurement stability, frequent calibration is not required.
HAFFMANS PORTABLE INTELLIGENT CO2 METER I-DGM
Fast and accurate determination of the CO2 content in beer and carbonated beverages based onHenry’s Law.
HAFFMANS CO2/O2 MEASUREMENT LABORATORY EQUIPMENT
Advanced CO2 and O2 measurement technology from your one stop supplier.
HAFFMANS PORTABLE OPTICAL CO2 /O2 /TPO METER C-DGM
Combining the internationally accepted determination of the dissolved CO2 content with a highly accurate dissolved O2 and TPO measurement.