- Home
- Case Studies
- St Austell
Industry
Brewing Industry
Challenge
Needed a more efficient filtration process.
Solution
Implementation of Pentair's BMF + Flux Compact S4 membrane filtration system.
Results
A sustainable solution, notable product quality improvements, reduced beer losses, and significant process gains.
ST AUSTELL - A BREWERY WITH A VISION
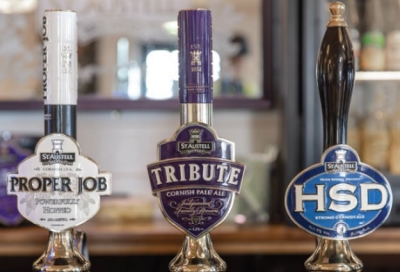
The town of St. Austell may be a point on the compass unfamiliar to many around the world, with some 20,000 inhabitants, nestled on the picturesque south coast of Cornwall, United Kingdom. While its original sustained economic prosperity was due to clay mining, today the town is best known as a tourist destination and, for beer drinkers with a keen sense of what’s temptingly tasty, there’s St. Austell Brewery.
Founded in 1851, the brewery prospered to the extent that as of 1893, it relocated to its current location, prominently on the hilltop above St. Austell. The brewery was situated about a mile uphill from the new railway line that gave it access to markets further afield than Cornwall. (And horses pulling wagons laden with heavy barrels of beer gave thanks that gravity worked in their favor.)
Today, over 20 years later, the story has played forward at pace. St. Austell Brewery has kept up with the accelerating trends in the brewing industry – and in many ways surpassed them.
St. Austell’s growth is being powered by several increasingly popular beers launched since his arrival in 1999. Tribute, a characterful premium ale, was the first to gain prominence in the brand portfolio. It has been joined recently by the aptly named Proper Job, a session strength IPA - and then there’s Korev, St. Austell’s lager brand launched in 2009 that has achieved the near-impossible, gaining sales against lagers backed by the considerable marketing spends of multinational brewers.
St. Austell has also distinguished itself from its regional family peer group by acquiring a nearby craft operation, Bath Ales, in 2016, subsequently announcing plans for a greenfield 60,000-hectoliter brewery that began production in May 2018. Currently, at St. Austell, the brewery is producing 213,000 hl annually on a 24/5 shift pattern. While cask ale still accounts for 50% of volumes, keg (17%) and bottled beers (30%) are driving growth, with cans starting to enter the mix.
None of this would have been possible without investing in the brewery and, when possible, preferring the latest in technology. St. Austell has been shrewd in making the most of what’s new and improving, especially as suppliers have been rolling out smaller capacity solutions suitable for mid-sized breweries. High on their must-have list was membrane-based filtration. It had been on the radar for some time, with neighboring cider makers using the technology for years.
In 2017, Pentair brought to market a Beer Membrane Filtration (BMF) range with hourly capacities between 60-85 hectoliters designed for brewers with annual outputs ranging from 10,000 hl up to 120,000 hl. And so following trials, in early 2018 Pentair’s 60 hl/h BMF + Flux Compact S4 came into service.
GAINS TIMES THREE
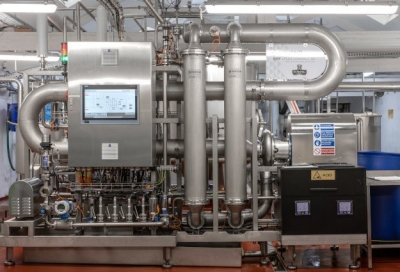
St. Austell’s partnership with Pentair originated well before its interest in membrane filtration, dating more than ten years when the first of what were to become many Pentair Südmo hygienic valves were installed.
Previously, the brewery operated with manually controlled valves. While they can have their advantages, manual control can have its drawbacks, mainly being their limited flexibility. Operators need to be present to make adjustments, potentially making process response times slower.
PARTNERS, PAST, PRESENT, AND FUTURE
St. Austell’s partnership with Pentair originated well before its interest in membrane filtration, dating more than ten years when the first of what were to become many Pentair Südmo hygienic valves were installed.
Previously, the brewery operated with manually controlled valves. While they can have their advantages, manual control can have its drawbacks, mainly being their limited flexibility. Operators need to be present to make adjustments, potentially making process response times slower.
So, gradually as the brewery automated its brewing process, automatic valves were needed to control the processes. The valve of choice was Südmo, based on its innovative hygienic and aseptic design & cleanability, helping to ensure St. Austell ensures that its brewing processes maintain strict hygiene standards.
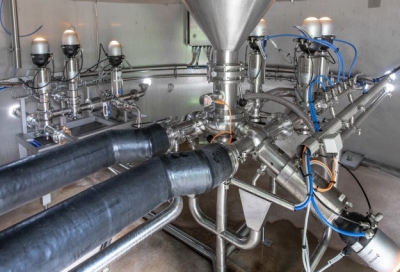
St. Austell Brewery has also been benefiting from the valves' durability, which aids in reducing maintenance-related downtime.
The absence of sumps and domes in Südmo valves helps to prevent any hidden areas where media could accumulate, ensuring easy cleaning and reliable operation.
What’s next for St. Austell Brewery? An area of further cooperation is potentially a CO2 recovery system. CO2 shortages in the United Kingdom have highlighted St Austell’s vulnerability. Along with the attractiveness of self-sufficiency, there’s also an environmental gain, with the amount of CO2 recaptured from fermentation equivalent to the requirements of the packaging line.
DOWNLOADS
Title | |
Case study: St. Austell | Download |
Related Products
Pentair's Proven Beer Membrane Filtration Technology saves operational costs to deliver the best and consitent beer quality and a predictable, constant output.
Benefit from our extensive range of stainless steel hygienic and aseptic valves, complete manifolds, and prefabricated units.
CO2 RECOVERY FOR BEVERAGE PRODUCERS
From fermentation sources or natural sparkling spring water, our solutions enable you to recover CO2 efficiently to safe, beverage-grade CO2.
Understanding Quality: discover Pentair Haffmans' CO2 management for better taste stability & longer shelf life of your beverage.