- Home
- Case Studies
- Paulaner
Industry
Brewing industry
Challenge
Increase filtration capacity
Solution
Five Pentair BMF +Flux Smart S8 skids designed for continuous filtration
Results
50% increase in filtration capacity
AN INTEGRAL PART OF GERMAN AND INTERNATIONAL BEER CULTURE
Paulaner Brewery is one of Munich’s oldest and well-known breweries. Its history is deeply rooted in the tradition of Bavarian beer culture and dates back to the 17th century.
The brewery’s name originates from the famous Paulaner monks who developed a unique beer called Salvator or “Savior” beer. As its popularity grew, the monks received permission to sell it to the public, leading to the establishment of the renowned Paulaner Brewery.
a rise in demand created a challenge
As preferences and trends in the beer industry continued to evolve, Paulaner's market preference shifted more towards filtered beers. In particular, demand for the Paulaner Münchner Hell rose and continues to rise rapidly, both nationally and internationally, so the brewery needed to increase its beer filtration capacity.
The previous filtration technology consisted of two Pentair Beer Membrane Filtration (BMF) blocks, which filtered alternately of one another. Each BMF block consisted of 4 skids, with 9 membrane pairs per skid. With a total of 705.6 m² filter area per BMF block, the maximum filter capacity was 400 hectoliters (hl) of filtered beer per hour.
Due to the good experience with the system, Paulaner decided to upgrade in consultation with Pentair. One of the challenges with the upgrade was replacing the old membrane filtration with the new system within just 3 weeks. To make this possible, dismantling and assembly were planned in advance together with the Paulaner project team.
Less downtime, less space required, yet more capacity
Paulaner replaced its eight Pentair BMF 18 semi-continuous skids with five Pentair BMF +Flux Smart S8 skids designed for continuous filtration.
Previously, the brewery could produce 32,500 HL per week within five days of operation, which corresponds to a capacity of 2 million HL of beer per year.
The new system can process 48,600 HL per week, resulting in a 50% increase in filtration capacity. This results in a higher operating index (OPI) and less filtration downtime.
The new system requires fewer modules, reducing the necessary footprint by 30%.
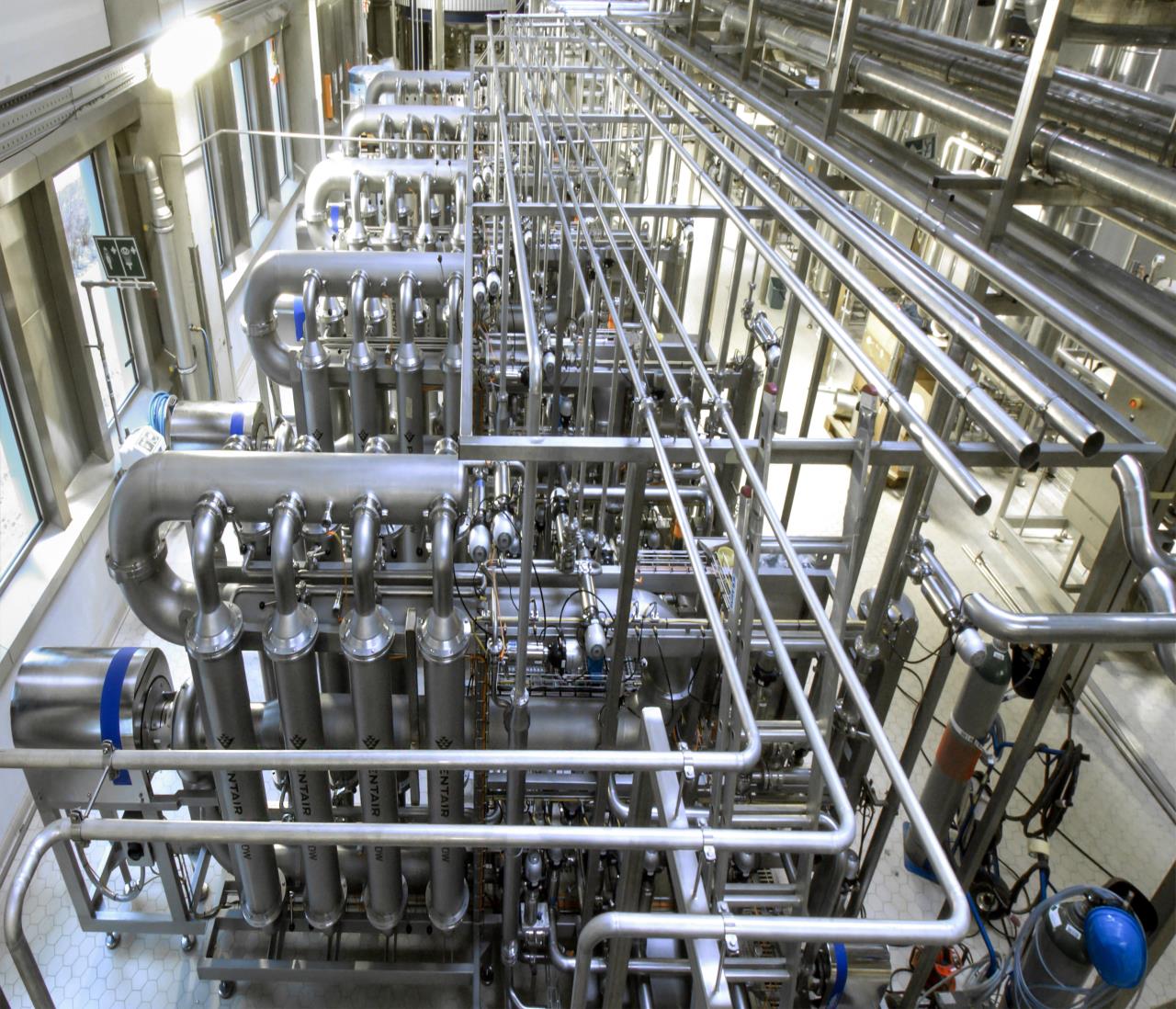
Why breweries insist on Pentair Beer Membrane Filtration Systems
Discover why a large German brewery choose the Pentair Beer Membrane Filtration System, the BMF +Flux Smart S8, and how it is enabling filtration automation, consistency in beer quality, and improving the sustainable footprint of the brewery.
CONTINUOUS FILTRATION
The heart of the Pentair BMF +Flux Smart S8 filter lies in its master controller and membrane units. These intelligent systems filter and clean independently, adapting to fluctuations in resource quality, which assists in maintaining peak efficiency . The system aids in reducing filtration downtime and product loss, coupled with an improvement in beer taste and sustainable practices.
Related Products
Beer Membrane Filtration System for large breweries that produce at a capacity between 200-900 hl/hr.