- Home
- Case Studies
- Alumina Refinery
background
The Bayer process is the most economical means of refining bauxite to alumina (aluminum oxide). The process involves the removal of organic components with the help of caustic soda in what is called a liquor burning plant. The liquor is concentrated by evaporation and combusted in a rotary kiln. This oxidizes the organics and produces a highly abrasive dust which needs to be filtered to prevent harmful emissions. In this case, the abrasion also caused filter elements to wear out prematurely.
process
At the liquor-burning process in an alumina refinery, process temperatures reach 900°C (1652 °F), while extraction takes place at 200°C (392°F).
Particulate nature and filter media
Abrasive particles are being filtered out with high-temperature PTFE membrane bags.
problem
Filter life was decreasing below six months, due to strong abrasive effects on the filter elements.
Frequent filter failures led to unwanted particulate emissions and action taken by the local EPA, with negative media attention as a result. The technical issue was basically a poor filter cleaning system design, resulting in negative cleaning over-pressure and, ultimately, no filter cleaning at all.
solution
Pentair applied the tried and tested GOCO software to improve the cleaning process, while the actual cleaning system was modified with GOCO nozzles and venturi nozzles.
This delivered multiple positive results for the refinery:
- Pulse cleaning operating pressure could be reduced
- Reduced power consumption of the liquor burner
- Filtration system downtime was eliminated
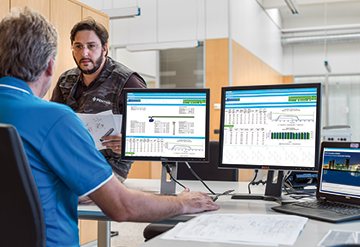